What is Inventory Control?
Replenishing your stock levels is a key part of running your business. Therefore, all businesses need to ensure their inventory control is up to scratch to maximize customer satisfaction.
Good inventory control management is more than regular trips to the wholesaler to buy more inventory. In day-to-day business, tasks will make ordering and purchasing stock difficult. This means forecasting, planning, implementing systems and backup systems to ensure your stock, and your reputation, is secure.
Inventory control definition
Inventory control and stock control both refer to the process of managing and maintaining a supply chain for a business. This tends to involve stock tracking on inventory management software (usually on the business's point of sale system) which records stock levels as sales are made. Managers keep this in check via a physical inventory count which can correct any discrepancies caused by wastage and damage, loss or theft.
Managing inventory also involves a system of reorder points where the business can typically expect stock to be replenished. For instance, many businesses get deliveries (or go out and buy stock) at regular, planned intervals during the week. This means if a product runs low, staff know more will arrive soon.
However, most businesses have further control systems in place to counteract fluctuations in customer demand. One of these is accepting the slight increase in wastage, loss and increased holding costs by keeping safety stock on essential products.
Safety stock is the purchasing of additional inventory to be held in reserve to prevent running short in the event of higher sales. It tends to be used only for a businesses more successful product lines and is often calculated using specialised formulas. These balance availability requirements with minimal holding costs and purchasing expenses to find a recommended stock figure.
Epos Now send out monthly software updates and look to make new partnerships at every opportunity to ensure businesses have the best chance to create the perfect bespoke setup to suit any enterprise:
- Streamline your sales setup to shave time during transactions and satisfy customers
- Manage inventory through barcodes, categories or previous lists, with flexible stock control technology
- Choose from hundreds of dedicated apps with business tools for every part of trade
- Receive business advice whenever you need it to get the most out of your system with an expert support team
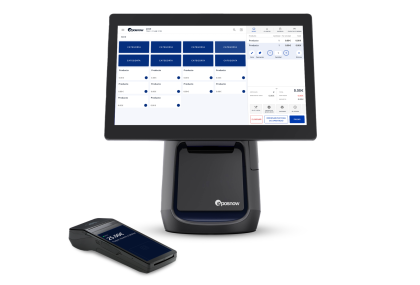
What is perpetual inventory control?
Perpetual inventory control is a management technique that fully utilises software inventory tracking by inputting stock delivery and deducting sales to perpetually maintain inventory levels.
With the advancement of EPOS (electronic point of sale) technology and integrated business software, more and more businesses (particularly retailers) have implemented perpetual inventory systems. The key advantage of these automated systems is the low maintenance involved which frees up time for staff to use on other tasks, and therefore reduces business expenses.
One drawback of perpetual inventory control is that while known wastage/stock depletion can be inputting into an EPOS, over time unknown variables such as theft can cause significant inaccuracies.
To counteract this, many businesses favour a hybrid inventory control, examples of which might involve carrying out stock counts on certain lines to confirm software levels are accurate. Over time, this would mean all lines have had physical inventory takes completed, but the advantage of low maintenance control of inventory is maintained.
How to anticipate inventory challenges
Managers tend to run into a number of similar inventory challenges, so it is possible to research and plan around these pitfalls:
Responsibility for stock control
The first and perhaps most important pitfall involves organisation of the management system. Who is responsible for maintaining stock levels? Does someone need a vehicle to go out and fetch materials, or is the supplier supposed to be delivering them? What about if there are supply issues? Who is doing which tasks?
Planning and structure are essential in stock management, and this is never more clear than during shortages. Businesses that run low on inventory can quickly descend into chaos, which is why anticipating challenges is so vital.
Any good inventory control system has contingency planning as well as every day structure. Physical stock checks are to be done by certain staff members at certain times. Delivery comes at certain times and can be signed for be staff of a certain level.
However, if delivery does not come, it is important for the business to have a driver they can rely on to go out, find and purchase the necessary stock. Alternatively, a staff member with a relationship with the supplier can help negotiate in difficult moments. It is also useful to have substitute products the business can recommend that customers may find a preferred alternative.
Mitigating losses
One of the great pains of inventory management is unnecessary wastage. Fluctuations in customer demand are an unavoidable part of business. However, staff members damaging goods before they reach the shelf, or putting newer stock out for sale before the old has sold can lead to unsaleable stock that cost the business valuable product.
For this reason, keeping a well-ordered storage area, with rules in place for stock rotation can prevent lost stock and reduce the risk of human error and clumsiness. Avoid clutter and keep the areas clean and tidy, not only to stay in line with health and safety, but to keep your inventory in perfect condition.
A good relationship with your supplier won’t always be enough to ensure you’re sent the best product. So having well-trained eyes (or even multiple staff members) checking goods and refusing less-than-perfect product can also make a big difference and will lower wastage.
Make better business decisions with Epos Now solutions
Managing and running your business is easier with technology that has every tool you need. Epos Now systems have hardware and software to suit your needs, generating hundreds of reports to help you know more about your business, and feel certain when the price is right.
Epos Now customers can:
- Create bespoke transaction setups on secure, speedy software to shave time off the sales process
- Choose from hundreds of apps and integrable partner programs to run accounting, marketing and other back-of-house functions in a way that suits you
- Access reports and inventory functionality on-site or off, night or day, through cloud technology
- Purchase all the retail or hospitality hardware and software and receive expert advice and support around the clock to get the best out of your business
To find out more about Epos Now solutions, submit your details below and speak to a member of our expert team.
With it's own in-built inventory system, Epos Now can streamline your business processes better than ever before, leaving you free to spend more time building your business.